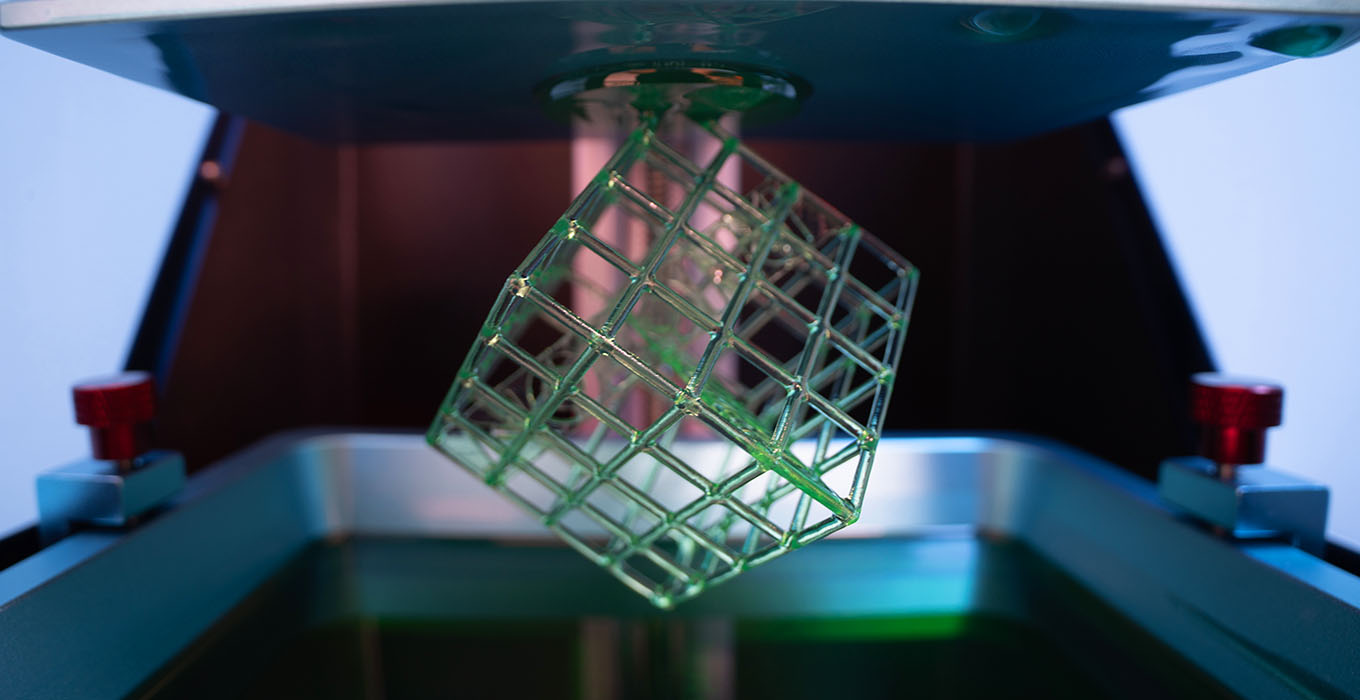
BLOG
Guide to 3D Printing II: FDM, SLA & SLS
Written by PHIL TSAO, FORMER DESIGN ENGINEER AT MISTYWEST
When we left off Part 1, we had just taken a look at the recent history of 3D printing technologies, and requested quotes from various vendors on a custom part to compare pricing for different technologies, and had introduced a chart that identifies the different materials available in these price points.
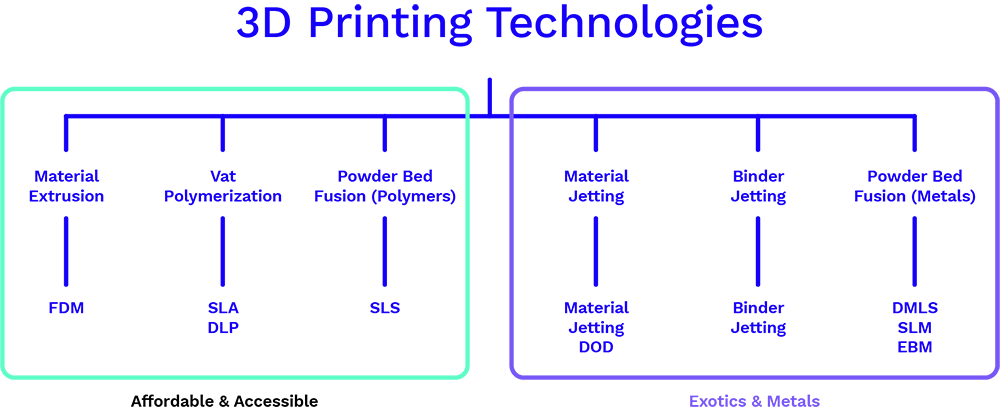
3D Printing Technologies: Affordable & Accessible to Exotics & Metals
Today, we explore what is available to makers in the Affordable & Accessible technologies. Whether you choose to bring these in internally or outsource to a rapid prototyping company, the following 3D printing techniques—FDM, SLA/DLP and SLS—can greatly accelerate product development through iteration to a tested, polished product much faster than ever before, and all at an affordable price.
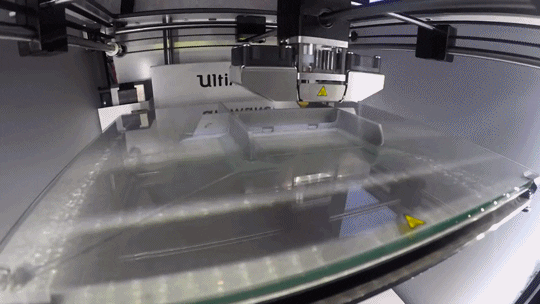
Source: Giphy
Fused Deposition Modelling (FDM)
While this technology is also known as Fused Filament Fabrication (FFF), the acronym FDM is a trademark of Stratasys. The most common and inexpensive form of 3D printing, FDM essentially consists of one or multiple extruders on a gantry which move across a build surface, squeezing out molten plastic melted from reels of filament.
Since the bulk of patents from Stratasys expired in 2013, these machines are now incredibly reliable and easy to use, and if you work with plastics at all, having an FDM printer is truly essential. Some great entry-level printers can be purchased from Ultimaker, Prusa Research, and Flashforge. For under $5000 CAD you can get a high quality, dual-extrusion machine with soluble supports (temporary structures used to enable printing sharp overhangs), and—with a little tweaking—can even get under-$2000 CAD printers working very reliably.
Recent innovations in FDM technology are allowing printers to extrude at very high temperatures—300°C and higher—opening up 3D printing to engineering thermoplastics such as Nylon, Polycarbonate, ULTEM and PEEK.
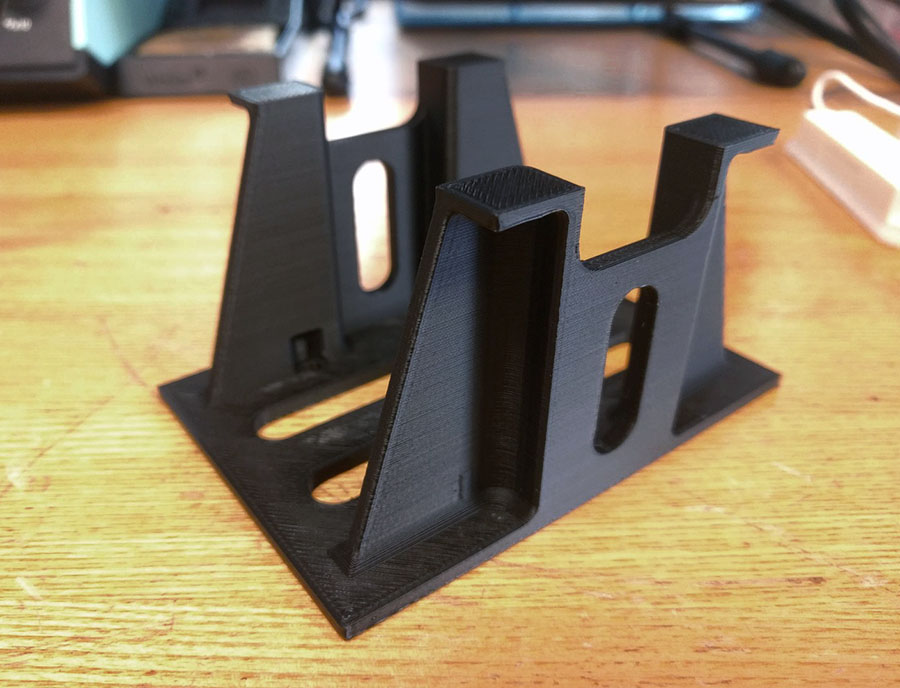
Image credit: Ember Prototypes
Pros and Cons of FDM:
+ Low cost
+ Easy to integrate machines into your company thanks to low cost, low maintenance and user friendly design
+ Uses real thermoplastics with actual material properties
+ Easy, soluble support cleanup
– Loose resolution (standard is 200um) and accuracy
– Parts are anisotropic (weak in layer adhesion)
– Poor surface finish
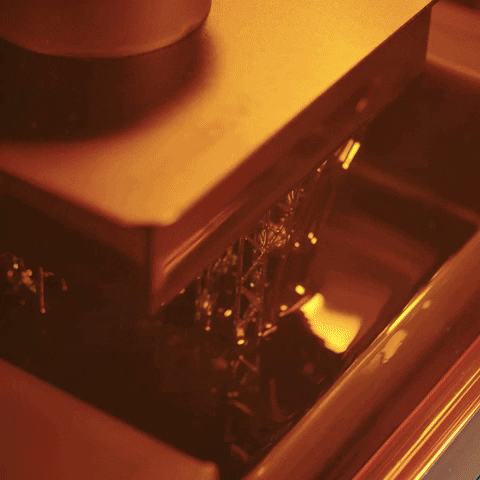
Source: Giphy
Stereolithography (SLA/DLP)
SLA is a form of 3D printing that takes advantage of a phenomenon called photopolymerization, where a light source of a specific wavelength (typically UV) is used to selectively cure liquid to create a solid object. Previously, SLA occurred with a laser, but developers on the cutting edge are using Digital Light Projection (DLP) and Liquid Crystal Displays (LCD) to achieve faster printing results (at the expense of aliasing artifacts and pixel resolution limitations, however). SLA is the second lowest cost 3D printing technique after FDM, and doesn’t have the anisotropic or surface finish issues that FDM has.
Peeling forces are important to consider when buying an SLA printer or outsourcing parts, as they can affect surface finish, material type, and failure probability (though these factors depend on part geometry as well).
There are two types of SLA: inverted and non-inverted. At the expense of introducing a peeling force between each cured layer of resin, inverted SLA (used by Formlabs) lends itself to smaller, less-expensive printers. Non-inverted SLA (dominated by 3D Systems) does not have peeling forces, which means less stress and deformation on materials, more material types, and smaller support structures.
Historically, SLA was limited to non-functional prototypes due to undesirable mechanical properties, but new materials are emerging which closely resemble real plastics like ABS, Polypropylene, Nylon and Silicone. One limitation is that most resins continue to have poorer impact and heat resistance than their thermoplastic counterparts, but thanks to ongoing advances in resin chemistry I predict this won’t be an issue within the next few years.
SLA post processing—consisting of washing excess resin and curing, and support structure removal—can take significant time. Support removal is more difficult in inverted systems as they require larger supports to prevent part breakage during the peeling process. Companies are actively working on a solution to this, focusing on polymerization prevention in a controlled thickness above the bottom of the resin tank, whether that’s through oxygen (Carbon), special materials (NewPro3D), or dual wavelengths & chemistry (University of Michigan).
SLA support removal
Aside from the limitations outlined above, the cost and accessibility of SLA is outstanding. Formlabs is the gold standard for prosumer printers, selling them for around $3,500 CAD. There are lower cost SLA printers available, however, they suffer from reliability, messiness, build volume and lack of engineering resins.
Prusa Research, famously known for their great FDM printers, has also recently released their own version of an LCD SLA printer, which can be purchased as a kit for under $1,500 CAD. With continuing innovations in hardware and material chemistry, SLA is becoming a very affordable way to prototype high quality, high resolution, functional parts.
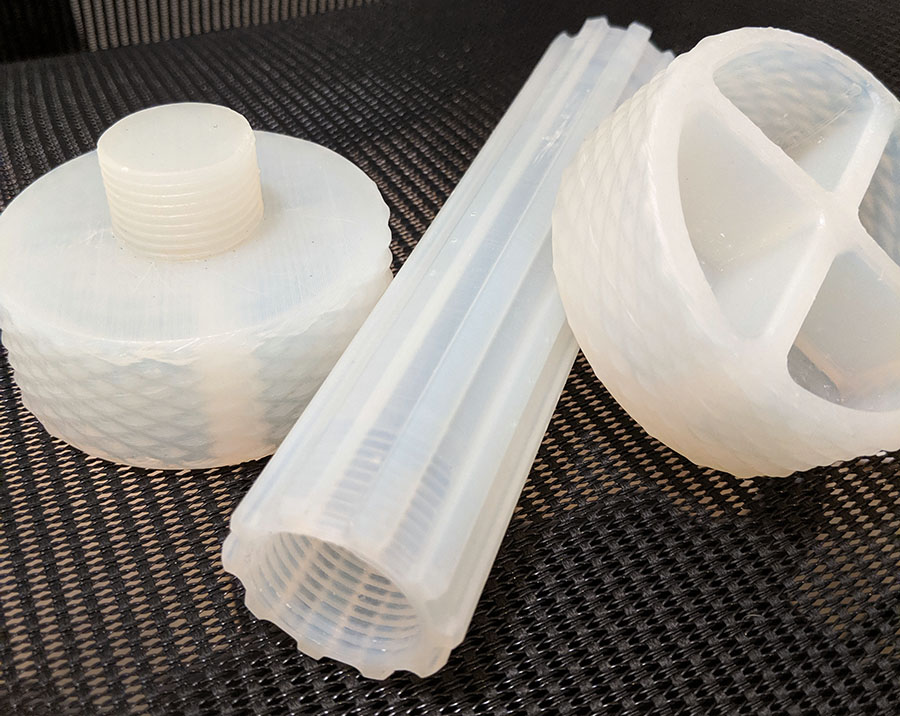
Image credit: Ember Prototypes
Pros and Cons of SLA:
+ Reasonable cost
+ Easy to integrate machines into your company
+ Exceptional resolution (25-100um), accuracy and surface finish
+ Isotropic properties
– Material property limitations (close simulations of real plastics)
– Post processing can be time consuming and messy
Selective Laser Sintering (SLS)
The last printing technology under Affordable & Accessible, SLS utilizes a laser and mirror galvanometer to sinter cross sections of polymer powder–typically Nylon–in a repeating process where the build platform moves down by a layer and new powder is spread across the part at a precise thickness, resulting in an isotropic part made of real Nylon.
Nylon has very good all-around mechanical and chemical resistance properties, good tensile strength, fair stiffness, high impact strength, and high heat deflection temperatures. SLS has good resolution and—at 100um, and combined with the Nylon materials—results in a smooth surface finish.
Due to the nature of powder sintering, the surface of SLS prints have a grainy texture and are inherently porous (roughly 30%). This porosity can be taken advantage of, however, through vacuum forming molds and dying of SLS parts to achieve a large range of colours.
Although SLS parts do not require supports—as the powder is self supporting—post processing of SLS is rather labour intensive; at the end of a print, the part must be removed and excavated from the block of powder, excess powder blown off the part, and further steps to cleanup are sometimes required.
Image credit: Stratasys
Outsourced SLS parts are reasonably priced and entry level printers are offered for around $10,000 CAD. However, low-cost SLS machines haven’t broken into product development and engineering the same way as FDM or SLA; partly because it is a newer technology, but also from higher capital cost, space required, cleanup, and tools needed for post processing.
I predict that in the coming years there will be new developments in post processing automation which will make SLS a more viable tool in engineering labs, with the cost of printers dropping too (though likely not to the same affordability as SLA or FDM machines).
Pros and Cons of SLS:
+ Reasonable cost
+ Great resolution (100um), accuracy and surface finish
+ Stronger & tougher thermoplastics than standard FDM
– Isotropic properties
– Not as easy to integrate machines into your engineering team
Conclusion to Part 2
Considering the price points for these affordable technologies, we are certainly living in the renaissance for prosumer 3D printing. Rapid prototyping, thanks to these techniques, allows for faster development of new, life-altering inventions, and empowers garage-scientists to experiment with greater ease.
In our next installment we will be covering Exotics & Metals, and the cool capabilities that these types of techniques can offer.